Brief overview of MIG welding
Metal Inert Gas (MIG) welding, also known as Gas Metal Arc Welding (GMAW), is a popular welding process that uses a continuously fed wire electrode and a shielding gas to melt and join pieces of metal. It is a versatile and easy-to-learn method that offers high productivity, making it a preferred choice for many industries.
The process of MIG welding involves the creation of an electric arc between the wire electrode and the metal workpiece. This arc heats the metal, causing it to melt and form a weld pool. The shielding gas, typically argon or a mixture of argon and carbon dioxide, protects the weld pool from contamination by the surrounding air.
MIG welding is known for its efficiency and versatility. It can be used on a wide range of metals and alloys, including mild steel, stainless steel, and aluminum, and is suitable for both thick and thin materials. It also allows for long, continuous welds, making it ideal for manufacturing and fabrication applications.
Our Top MIG Welder Picks
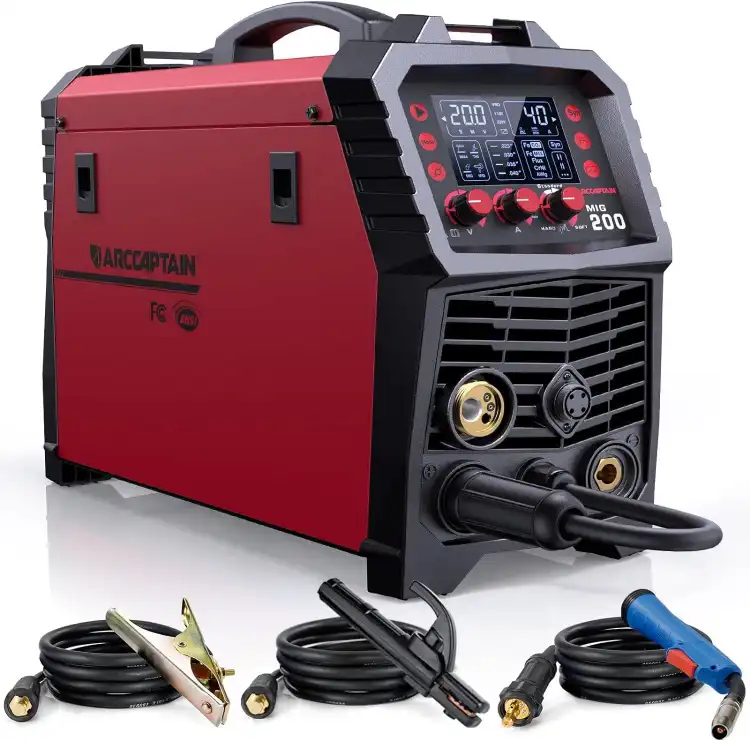
ARCCAPTAIN MIG Welder
Check on AmazonKey Specs
- Welding Processes: MIG, Flux Core, Stick, Spot, Lift TIG
- Wire Compatibility: Solid wire, flux core wire, aluminum wire
- Cooling System: Fan operates on demand
- Display: Large LED screen for easy data reading
- Safety Features: VRD, over-current, over-voltage, overload, overheating protection
The ARCCAPTAIN MIG Welder is a 6-in-1 multi-process welding machine, offering Gas/Solid Wire MIG, Gasless Flux Core MIG, Stick/MMA, Spot Welding, and Lift TIG, meeting a variety of welding needs. It supports multiple wire sizes, including solid and flux core wires, and an optional spool gun connector. The synergic MIG feature ensures automatic adjustment for optimal results, and you can customize the welding current. The large LED display makes it easy to monitor welding data without removing your helmet. With additional features like adaptive crater and burn-back adjustment, it provides superior efficiency. It’s portable, durable, and packed with safety functions, making it perfect for professionals and DIY enthusiasts alike.
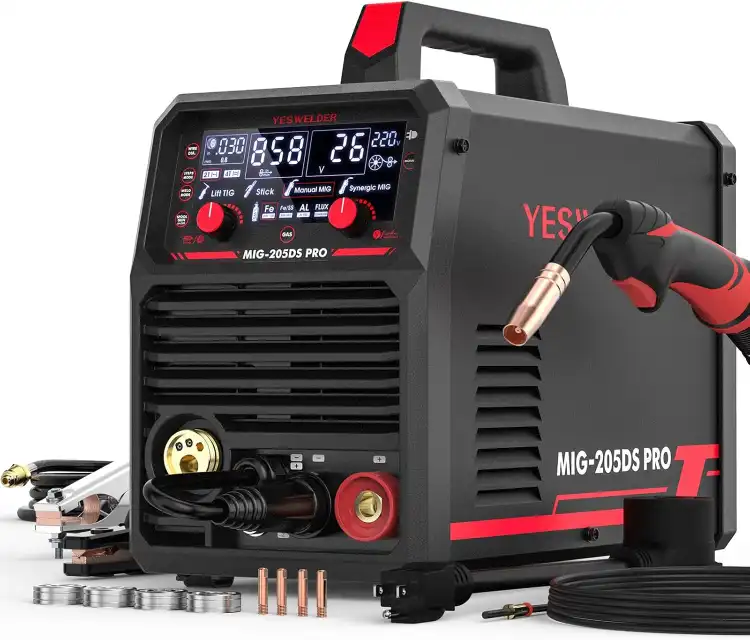
YESWELDER MIG-205DS PRO MIG Welder
Check on AmazonKey Specs:
- Welding Processes: MIG, Flux Core, Stick, Lift TIG, Spool Gun
- Max Output: 205 amps
- Technology: IGBT Inverter for stable performance
- Display: Digital display for improved clarity
- Safety Features: Over-current, over-voltage, and over-heating protection
The YESWELDER MIG-205DS PRO MIG Welder is a 5-in-1 machine that supports Gas MIG, Flux Core MIG, Spool Gun MIG, Lift TIG, and Stick welding. It features IGBT inverter technology for smooth, stable performance and a digital display for enhanced clarity. Synergic control adjusts voltage and wire feeding speed automatically, making it suitable for various thicknesses. It is spool gun compatible for aluminum welding, ensuring smooth wire feeding. The machine also includes multiple safety features, including over-current, over-voltage, and overheating protection, prioritizing user safety.
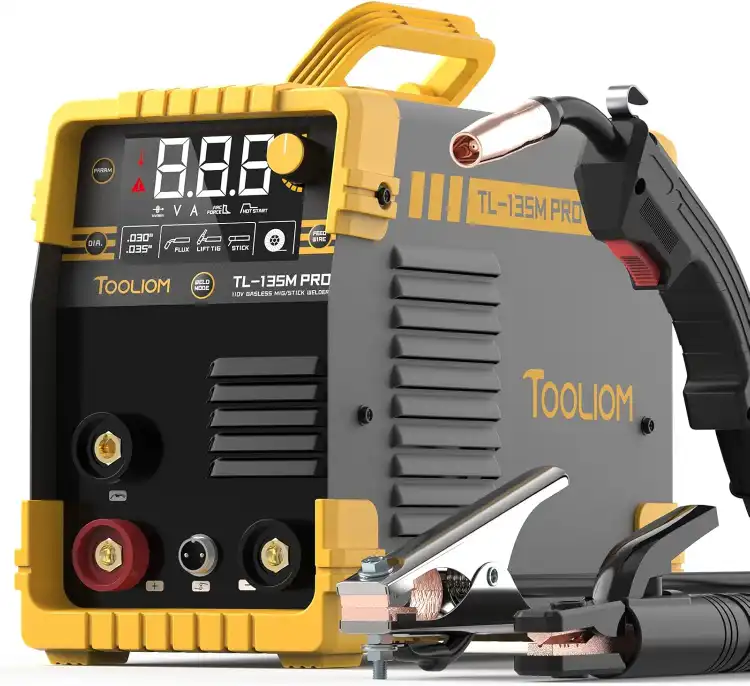
TOOLIOM 135A MIG Welder Flux Core 110V MIG Welder
Check on AmazonKey Specs:
- Welding Processes: Flux MIG, Stick, Lift TIG
- Max Output: 135 amps
- Welding Material: Mild steel up to 1/8 inch
- Wire Compatibility: .030” & .035” flux core wire
- Power Source: Standard 110V household voltage
The TOOLIOM 135A MIG Welder is a versatile machine offering Flux Core MIG, Stick, and Lift TIG welding capabilities. With a 135A output current, it can easily weld mild steel up to 1/8 inch (3.0mm) in thickness and is compatible with .030” & .035” flux core wire. The welder features an intelligent LCD panel for easy monitoring of welding data and synergic control, which adjusts wire feeding speed automatically. It operates on standard 110V household voltage, making it convenient for various settings. Note that the Lift TIG torch is sold separately.
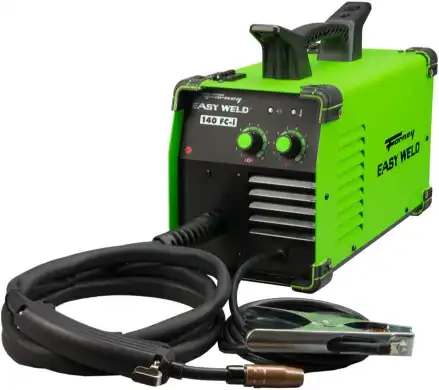
FORNEY Easy Weld 140 Amp 120-Volt Flux-Cored Wire Feed Welder
Check on AmazonKey Specs:
- Max Output: 140 amps
- Welding Capacity: Mild steel up to 1/4 inch
- Wire Compatibility: 0.030-inch flux-core wire
- Portability: Weighs 19 pounds
- Power Source: 120V, 20 AMP breaker required
The FORNEY Easy Weld 140 Amp 120-Volt Flux-Cored Wire Feed Welder is an excellent option for DIY enthusiasts and beginners. It features infinite voltage and wire feed speed control, allowing you to adjust and achieve perfect welds every time. With a 140 AMP output, it can weld mild steel up to 1/4 inch and supports both 2 and 10-pound rolls of flux-core wire. This lightweight welder weighs only 19 pounds, making it easily portable for various projects. It doesn’t require gas, making it highly convenient and cost-effective. Standard household power (at least a 20 AMP breaker) is sufficient for operation.
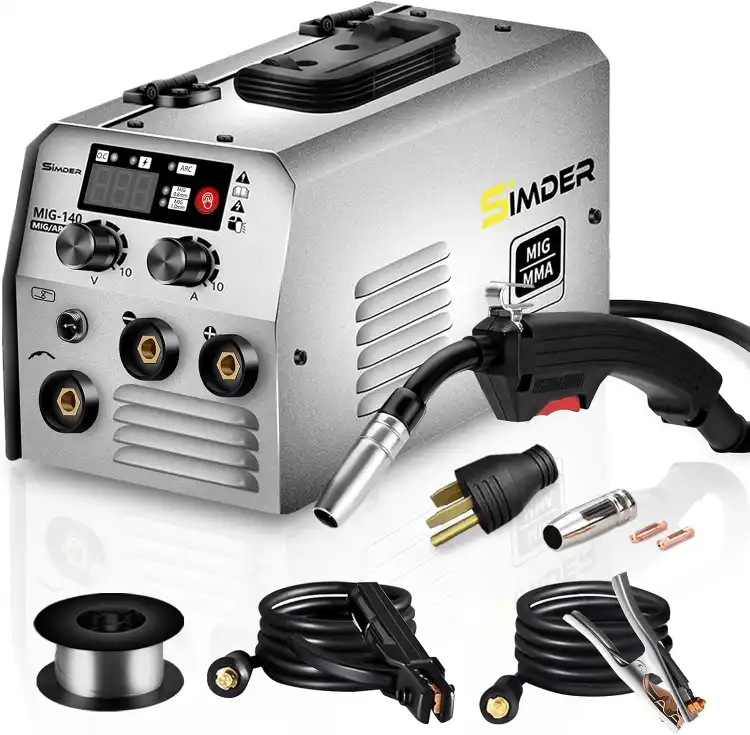
SSIMDER MIG Welder
Check on AmazonKey Specs:
- Max Output: 145 amps
- Voltage: Dual voltage (110V/220V)
- Welding Types: MIG (Flux core), ARC
- Wire Sizes: 0.030″ and 0.035″ flux core
- Included Accessories: MIG torch, electrode holder, ground clamp, 110V/220V adapter
The SSIMDER MIG Welder is a powerful and versatile 2-in-1 welding machine that supports both MIG and ARC welding. It delivers a maximum output of 145 amps and works on dual voltage (110V/220V), allowing for flexible operation. Its Synergic mode automatically adjusts voltage based on current, making it beginner-friendly and easy to use. The welder handles flux-cored wires in sizes 0.030″ and 0.035″, and it can also weld with E7018 and E6013 electrodes in ARC mode. With the inclusion of all necessary accessories, including a MIG torch, electrode holder, and ground clamp, it’s ready for a variety of welding applications, from repairs to DIY projects.
Importance of choosing the right MIG welder
Choosing the right MIG welder is crucial for achieving high-quality welds. The right welder not only ensures the efficiency and effectiveness of the welding process but also contributes to the safety and longevity of the equipment. Therefore, it is important to consider various factors such as power output, duty cycle, wire feed speed, and thermal overload protection when choosing a MIG welder.
Furthermore, the type of MIG welder you choose should align with your specific welding needs. For instance, if you are working with thick materials, you would need a welder with a higher power output. Similarly, if you are planning to use the welder for extended periods, you would need a welder with a longer duty cycle.
Lastly, the brand and price of the MIG welder are also important considerations. Different brands offer different features and quality levels, and the price can vary significantly. Therefore, it is important to do thorough research and compare different options before making a decision.
Understanding MIG Welding
Definition of MIG welding
MIG welding, or Metal Inert Gas welding, is a semi-automatic or automatic arc welding process in which a continuous and consumable wire electrode and a shielding gas are fed through a welding gun. The electric arc formed between the wire electrode and the metal workpiece melts the workpiece and the electrode, creating a weld pool that cools to form a joint.
The term “MIG welding” comes from the use of an inert gas, typically argon or helium, as the shielding gas. However, in practice, a mixture of argon and active gases such as carbon dioxide or oxygen is often used. Therefore, the process is also referred to as Gas Metal Arc Welding (GMAW).
One of the key advantages of MIG welding is its versatility. It can be used on a wide range of metals and alloys, and is suitable for both manual and mechanized welding. It also allows for long, continuous welds, making it ideal for manufacturing and fabrication applications.
Basic principles of MIG welding
The basic principle of MIG welding is the creation of an electric arc between a continuously fed wire electrode and the metal workpiece. This arc generates intense heat, which melts the metal and forms a weld pool. The shielding gas protects the weld pool from contamination by the surrounding air, ensuring the formation of a clean, strong weld.
The wire electrode serves a dual role in MIG welding. It not only conducts the electric current that generates the arc but also provides filler metal for the weld. As the electrode melts, it is deposited into the weld pool, filling the gap between the pieces of metal being joined.
The quality of a MIG weld is largely determined by the stability of the arc and the cleanliness of the weld pool. Therefore, it is important to maintain a consistent arc length and to use a suitable shielding gas. The speed of the wire feed and the power output of the welder also play a crucial role in the welding process.
Common uses of MIG welding
MIG welding is widely used in a variety of industries due to its versatility and efficiency. It is commonly used in the automotive industry for the manufacturing and repair of vehicles. It is also used in the construction industry for the fabrication of steel structures and in the shipbuilding industry for the construction of ships.
In addition to these industrial applications, MIG welding is also popular in smaller scale operations such as home workshops and art studios. Its ease of use and adaptability make it a preferred choice for DIY enthusiasts and artists working with metal.
Furthermore, MIG welding is often used in vocational training programs as it is relatively easy to learn and provides a solid foundation for other welding techniques. It is also a valuable skill for those interested in careers in industries such as manufacturing, construction, and automotive repair.
Types of MIG Welders
Power source-based classification
MIG welders can be classified based on their power source into two main types: transformer-based welders and inverter-based welders. Transformer-based welders use a traditional transformer to convert the input power to the required output. They are known for their durability and reliability, but they are also heavy and less energy-efficient.
Inverter-based welders, on the other hand, use modern inverter technology to convert the input power. They are lighter and more energy-efficient than transformer-based welders, and they also offer better control over the welding parameters. However, they are generally more expensive and may not be as durable.
When choosing between a transformer-based welder and an inverter-based welder, it is important to consider your specific welding needs. If you need a robust and reliable welder for heavy-duty applications, a transformer-based welder may be a good choice. If you need a lightweight and portable welder for light-duty applications, an inverter-based welder may be more suitable.
Metal thickness-based classification
MIG welders can also be classified based on the thickness of the metal they can weld. Light-duty welders are designed for welding thin materials, typically up to 1/8 inch thick. They are suitable for small repairs and hobbyist applications. Medium-duty welders can handle materials up to 1/4 inch thick and are suitable for general fabrication and construction applications.
Heavy-duty welders, also known as industrial welders, can weld materials up to 1/2 inch thick or more. They are designed for heavy fabrication and manufacturing applications. The choice of a light-duty, medium-duty, or heavy-duty welder depends on the thickness of the materials you plan to weld and the intensity of the welding tasks.
It is important to note that the thickness of the metal is not the only factor to consider when choosing a MIG welder. Other factors such as the type of metal, the desired weld quality, and the available power supply also play a crucial role.
Functionality-based classification
Another way to classify MIG welders is based on their functionality. Some welders offer basic MIG welding functionality, while others offer additional functionalities such as flux-cored arc welding (FCAW), stick welding (SMAW), and TIG welding (GTAW).
Multi-process welders that offer MIG, TIG, and stick welding functionalities are popular for their versatility. They allow you to switch between different welding processes as needed, making them a cost-effective choice for those who need to perform different types of welding tasks.
However, multi-process welders may not offer the same level of performance and control as dedicated MIG welders. Therefore, if you primarily perform MIG welding and require high-quality welds, a dedicated MIG welder may be a better choice.
Key Features to Consider When Buying a MIG Welder
Power output
The power output of a MIG welder, measured in amperes (A), is one of the most important features to consider. It determines the thickness of the metal that the welder can handle. A higher power output allows for welding thicker materials, while a lower power output is suitable for welding thinner materials.
Most MIG welders have a variable power output, allowing you to adjust the power according to the thickness of the metal and the desired weld quality. However, it is important to note that the maximum power output of the welder should align with your welding needs. For instance, if you plan to weld thick materials, you would need a welder with a high maximum power output.
Another important factor to consider is the power supply. MIG welders can run on either 110V or 220V power supply. A 110V welder is suitable for light-duty applications, while a 220V welder is needed for heavy-duty applications. Some welders offer dual voltage capability, allowing you to switch between 110V and 220V as needed.
Duty cycle
The duty cycle of a MIG welder refers to the amount of time the welder can operate continuously in a 10-minute period without overheating. It is expressed as a percentage. For instance, a duty cycle of 20% means that the welder can operate continuously for 2 minutes and then needs to cool down for 8 minutes.
A longer duty cycle allows for longer continuous welding, making it ideal for heavy-duty applications. However, a longer duty cycle also means a higher price. Therefore, it is important to choose a welder with a duty cycle that matches your welding needs and budget.
It is also worth noting that the duty cycle is usually specified at a certain power output. For instance, a welder may have a duty cycle of 20% at 200A and a duty cycle of 60% at 150A. Therefore, it is important to consider both the power output and the duty cycle when choosing a MIG welder.
Wire feed speed
The wire feed speed of a MIG welder refers to the speed at which the wire electrode is fed through the welding gun. It is usually adjustable and is measured in inches per minute (IPM) or meters per minute (MPM). The wire feed speed plays a crucial role in the welding process as it affects the stability of the arc and the quality of the weld.
A higher wire feed speed results in a larger weld bead and a higher deposition rate, making it suitable for welding thick materials. A lower wire feed speed results in a smaller weld bead and a lower deposition rate, making it suitable for welding thin materials.
Some MIG welders offer automatic wire feed speed adjustment, which automatically adjusts the wire feed speed based on the power output. This feature can be helpful for beginners who are not yet familiar with the relationship between the wire feed speed and the welding parameters.
Thermal overload protection
Thermal overload protection is a safety feature that prevents the welder from overheating. When the welder reaches a certain temperature, the thermal overload protection system automatically shuts off the welder to allow it to cool down. This not only protects the welder from damage but also enhances the safety of the welding process.
Most modern MIG welders come with thermal overload protection. However, the sensitivity and response time of the system can vary. A good thermal overload protection system should respond quickly to prevent overheating and should also have a short recovery time to minimize downtime.
It is also worth noting that the need for thermal overload protection depends on the intensity of the welding tasks. If you plan to use the welder for extended periods, a robust thermal overload protection system is essential. If you only use the welder occasionally for short periods, a basic thermal overload protection system may be sufficient.
Understanding the Specifications of MIG Welders
Importance of reading and understanding specifications
Reading and understanding the specifications of MIG welders is crucial for making an informed purchase decision. The specifications provide detailed information about the capabilities and features of the welder, allowing you to assess whether it meets your welding needs.
Some of the key specifications to look for include the power output, duty cycle, wire feed speed, and thermal overload protection. These specifications directly affect the performance and safety of the welder. Other important specifications include the type of shielding gas, the wire size, and the weight and dimensions of the welder.
It is also important to understand the terminology used in the specifications. For instance, the term “duty cycle” refers to the amount of time the welder can operate continuously without overheating, while the term “wire feed speed” refers to the speed at which the wire electrode is fed through the welding gun. Familiarizing yourself with these terms will help you interpret the specifications correctly.
Explanation of common specifications
The power output of a MIG welder, measured in amperes (A), indicates the maximum current that the welder can produce. A higher power output allows for welding thicker materials. The power output is usually variable, allowing you to adjust the current according to the thickness of the metal and the desired weld quality.
The duty cycle of a MIG welder, expressed as a percentage, indicates the amount of time the welder can operate continuously in a 10-minute period without overheating. A higher duty cycle allows for longer continuous welding. The duty cycle is usually specified at a certain power output.
The wire feed speed of a MIG welder, measured in inches per minute (IPM) or meters per minute (MPM), indicates the speed at which the wire electrode is fed through the welding gun. A higher wire feed speed results in a larger weld bead and a higher deposition rate.
Thermal overload protection is a safety feature that prevents the welder from overheating. When the welder reaches a certain temperature, the thermal overload protection system automatically shuts off the welder to allow it to cool down.
MIG Welder Brands
Overview of popular MIG welder brands
There are several popular brands that manufacture MIG welders, each offering a range of models with different features and capabilities. Some of the most well-known brands include Miller, Lincoln Electric, Hobart, and ESAB.
Miller is a leading manufacturer of welding equipment and is known for its high-quality MIG welders. The company offers a wide range of models, from entry-level welders for beginners and hobbyists to professional-grade welders for industrial applications.
Lincoln Electric is another reputable brand that offers a variety of MIG welders. The company is known for its innovative technology and durable products. Its MIG welders are popular for their performance and ease of use.
Hobart is a brand that is known for its reliable and affordable MIG welders. The company offers a range of models that are suitable for both home use and light industrial applications.
ESAB is a global leader in the welding industry and offers a wide range of MIG welders. The company is known for its advanced technology and high-quality products.
Comparison of brands based on quality, price, and features
When comparing MIG welder brands, it is important to consider the quality, price, and features of their products. Miller and Lincoln Electric are known for their high-quality welders that offer advanced features and reliable performance. However, their products are also typically more expensive.
Hobart and ESAB offer more affordable options without compromising on quality. Their welders are reliable and easy to use, making them a popular choice for beginners and hobbyists. However, they may not offer the same level of performance and advanced features as Miller and Lincoln Electric.
When comparing features, it is important to consider your specific welding needs. If you need a welder for heavy-duty applications, you may want to opt for a brand that offers high power output and a long duty cycle. If you need a welder for light-duty applications, a brand that offers a compact and lightweight design may be more suitable.
Price Range of MIG Welders
Factors affecting the price of MIG welders
The price of MIG welders can vary significantly based on several factors. One of the main factors is the power output. Welders with a higher power output are typically more expensive as they can handle thicker materials and more demanding welding tasks.
The duty cycle is another factor that affects the price. Welders with a longer duty cycle are more expensive as they can operate for longer periods without overheating. The type of power source also affects the price. Inverter-based welders are generally more expensive than transformer-based welders due to their advanced technology and energy efficiency.
Additional features such as thermal overload protection, automatic wire feed speed adjustment, and multi-process capability can also increase the price. The brand and model of the welder also play a role. Well-known brands that are known for their quality and reliability often command a higher price.
Average price range for different types of MIG welders
The price of MIG welders can range from a few hundred dollars to several thousand dollars. Entry-level welders for beginners and hobbyists typically cost between $200 and $500. These welders usually have a lower power output and a shorter duty cycle, but they are sufficient for light-duty applications and small repairs.
Mid-range welders for general fabrication and construction applications typically cost between $500 and $1,000. These welders have a higher power output and a longer duty cycle, allowing for more demanding welding tasks.
High-end welders for heavy-duty industrial applications typically cost over $1,000. These welders offer the highest power output and the longest duty cycle, and they often come with advanced features such as thermal overload protection and automatic wire feed speed adjustment.
Where to Buy MIG Welders
Buying from physical stores vs. online
There are two main options for buying MIG welders: physical stores and online. Buying from a physical store allows you to see and touch the welder before making a purchase. You can also ask the store staff for advice and recommendations. However, the selection of welders may be limited, and the prices may be higher due to the overhead costs of running a physical store.
Buying online offers a wider selection of welders and often lower prices. You can also read customer reviews and compare different models and brands easily. However, you cannot see or touch the welder before making a purchase, and you may have to pay for shipping. It is also important to buy from a reputable online retailer to ensure the quality and authenticity of the welder.
Whether you choose to buy from a physical store or online, it is important to do thorough research and compare different options before making a decision. You should also consider the warranty and after-sales service offered by the seller.
Recommended online platforms for buying MIG welders
There are several online platforms where you can buy MIG welders. Some of the most popular ones include Amazon, eBay, and the websites of the welder manufacturers. These platforms offer a wide selection of welders and often have customer reviews that can help you make an informed decision.
Amazon is a popular choice due to its vast selection of products and reliable customer service. You can find welders from all the major brands, and you can also read customer reviews and Q&As to learn more about the products.
eBay is another good option, especially if you are looking for used or discounted welders. However, it is important to check the seller’s feedback and return policy before making a purchase.
The websites of the welder manufacturers often offer the most detailed information about the products. They also offer customer support and after-sales service. However, the prices may be higher than on other platforms.
Safety Precautions When Using MIG Welders
Importance of safety when welding
Safety is paramount when welding. The welding process involves high temperatures, electric currents, and intense light, all of which can pose serious risks if not handled properly. Therefore, it is important to follow safety precautions to protect yourself and others around you.
One of the main risks when welding is the exposure to intense light, which can cause eye damage. Therefore, it
FAQ
What is a MIG welder?
A MIG welder (Metal Inert Gas welder) is a type of welding machine that uses a continuous wire feed and an inert gas to create a strong bond between metal parts.
How does a MIG welder work?
It feeds a wire electrode through a welding gun, which melts and joins metal pieces together, while an inert gas protects the weld from contamination.
What are the benefits of using a MIG welder?
MIG welding is fast, easy to learn, and ideal for welding thin to medium-thickness metals, providing clean and strong welds with minimal spatter.
Can a MIG welder be used on all metals?
MIG welders are most commonly used on mild steel, stainless steel, and aluminum, but the right wire and gas mixture are needed for different metals.
Is a MIG welder suitable for beginners?
Yes, MIG welding is often recommended for beginners due to its straightforward operation and versatility for various welding projects.