Wire soldering is a fundamental skill in the world of electronics, playing a crucial role in the creation of durable and reliable electrical connections. It is a process that involves the use of a filler material, known as solder, to join together two or more metal items. The importance of wire soldering cannot be overstated, as it is a key factor in ensuring the longevity and functionality of electronic devices.
The purpose of this article is to provide a comprehensive guide on wire soldering. It aims to educate readers about the basics of wire soldering, the factors to consider when buying wire solder, and how to properly use and maintain wire solder. Additionally, it will discuss the common mistakes to avoid when buying wire solder, provide a case study on the successful use of wire solder, and explore future trends in wire soldering.
By the end of this article, readers should have a solid understanding of wire soldering and be able to make informed decisions when purchasing and using wire solder. This knowledge will be invaluable for anyone involved in electronics, whether they are hobbyists, professionals, or students.
Our Top Wire Solder Picks
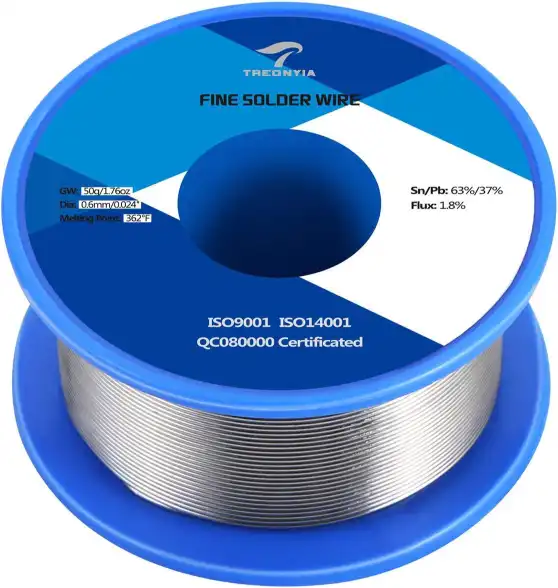
TREONYIA 63-37 Tin Lead Rosin Core Solder Wire for Electrical Soldering
Check on AmazonKey Specs:
- Diameter: 0.6mm (0.0236 inches)
- Composition: Tin 63%, Lead 37% (Sn63-Pb37)
- Flux Content: 1.8%
- Melting Point: 361℉ (183℃)
- Weight: 0.11lbs (50g)
The TREONYIA 63-37 Tin Lead Rosin Core Solder Wire is an excellent choice for electrical soldering projects, offering high-quality performance with minimal smoke and rosin splash. Its low melting point of 361℉ (183℃) ensures quick and efficient soldering, making it ideal for both DIY and professional use. With a 0.6mm diameter, it provides precise application, and the flux content of 1.8% ensures superior electrical insulation and excellent flowability. It’s perfect for soldering cables, radios, circuit boards, and more.
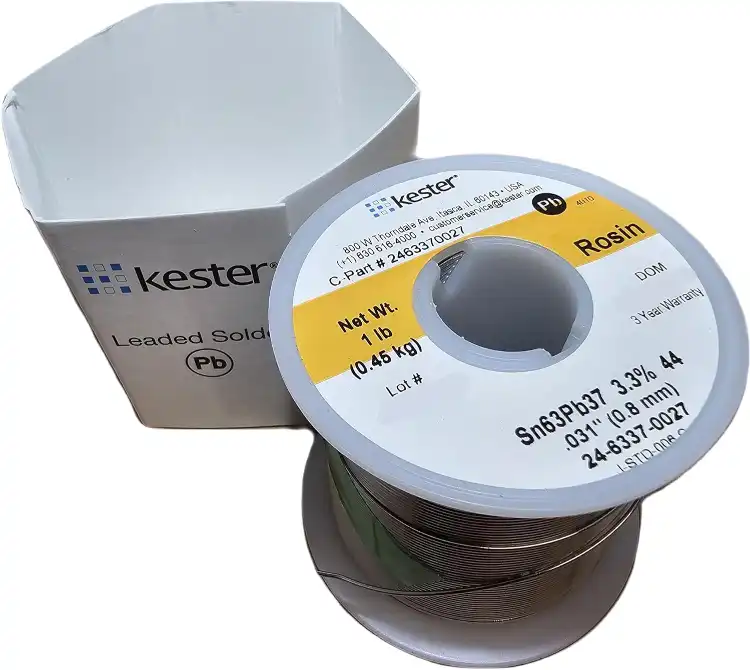
KESTER SOLDER 24-6337-0027 Solder Wire
Check on AmazonKey Specs:
- Diameter: 0.80mm (0.031 inches)
- Composition: 63% Tin / 37% Lead
- Melting Point: 183°C
- Weight: 1lb spool
- Halogen: Product contains halogen
The Kester 24-6337-0027 Solder Wire is an excellent choice for both professionals and hobbyists seeking reliable and efficient soldering. With a 63/37 tin/lead alloy, this solder provides optimal flow and fast wetting, making it ideal for precision work. The 0.80mm diameter ensures a smooth application, and the 183°C melting point allows for quick, clean soldering. As a trusted brand in the industry, Kester’s solder wire ensures strong, durable connections for a wide range of electrical projects.
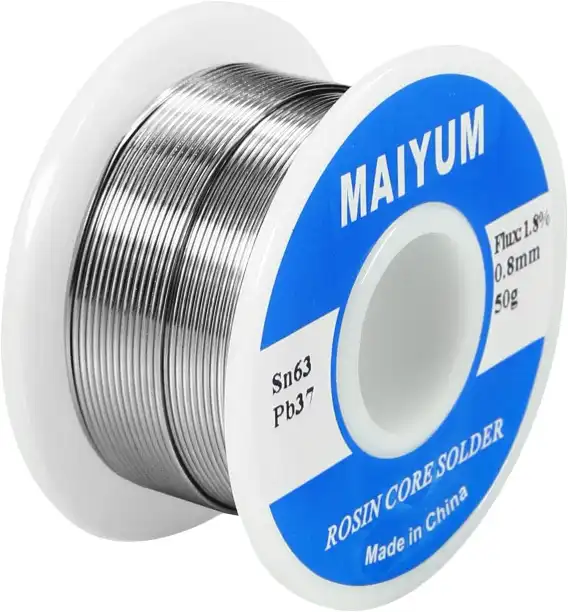
63-37 Tin Lead Rosin Core Solder Wire for Electrical Soldering
Check on AmazonKey Specs:
- Diameter: 0.8mm (0.0315 inches)
- Composition: 63% Tin / 37% Lead
- Flux Content: 1.8%
- Melting Point: 361°F / 183°C
- Weight: 50g (0.11 lbs)
The MAIYUM 63/37 Tin Lead Rosin Core Solder Wire is a fantastic choice for various electrical soldering tasks. With a flux content of 1.8% and a low melting point of 361°F (183°C), it ensures smooth flow and quick soldering for strong, reliable joints. The 0.8mm diameter is ideal for precision work, whether you’re repairing circuit boards, cables, or electronics like radios and toys. This solder wire provides consistent performance and is highly praised for its excellent solderability.
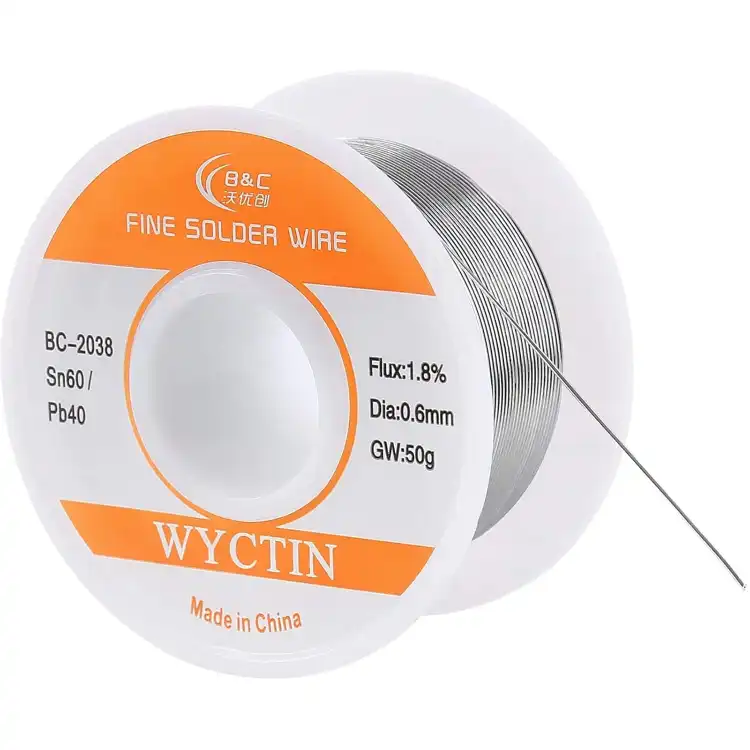
WYCTIN 60-40 Tin Lead Rosin Core Solder Wire for Electrical Soldering
Check on AmazonKey Specs:
- Composition: 60% Tin / 40% Lead
- Diameter: 0.6mm (0.0236 inches)
- Flux Content: 1.8%
- Melting Point: 361°F / 183°C
- Weight: 50g (0.11 lbs)
The WYCTIN 60-40 Tin Lead Rosin Core Solder Wire is an excellent choice for anyone involved in electrical soldering. With a 0.6mm diameter, it’s perfect for precision tasks like circuit board repairs or DIY projects. Its low melting point of 361°F (183°C) ensures smooth flow, allowing for quick and clean soldering. The 1.8% flux content also guarantees minimal residue, leaving your work neat. This wire is highly versatile and works well with a variety of electrical devices, from cables to small appliances.
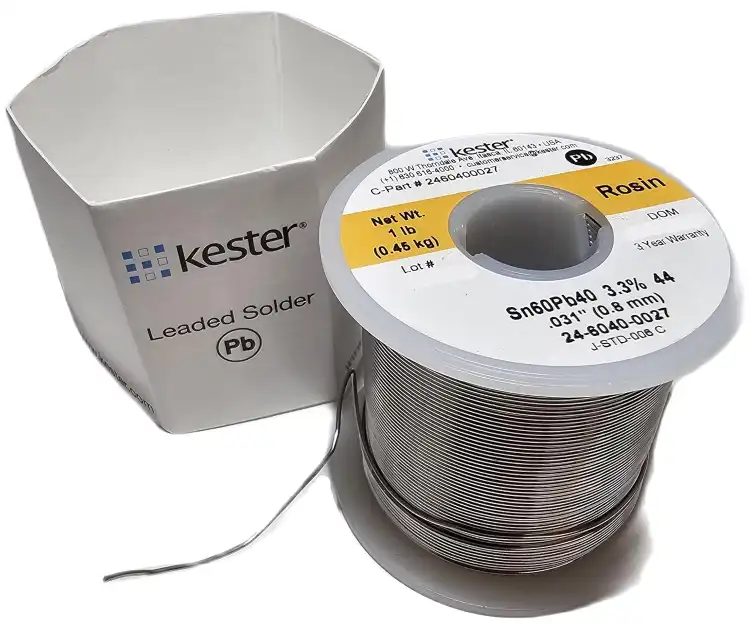
KESTER SOLDER 24-6040-0027 Wire Solder
Check on AmazonKey Specs:
- Diameter: 0.031″ (0.80mm)
- Alloy: 60% Tin / 40% Lead
- Flux: 44 Rosin Flux (3.3%)
- Weight: 1 Pound per spool
- Made in: U.S.A.
The Kester 24-6040-0027 Wire Solder is a top-tier choice for professionals and hobbyists alike. With a 0.031″ diameter and a 60/40 tin-lead alloy, it ensures reliable and strong solder joints. The 44 Rosin Flux (3.3%) aids in smooth, efficient soldering with minimal residue. This solder wire offers great flowability and superior wetting action, making it ideal for high-quality electrical work. Its authenticity as a U.S.-made Kester product guarantees performance and consistency in every spool.
Understanding Wire Soldering
Wire soldering is a technique used to join together two or more metal items by melting a filler material, known as solder, onto the joint. The solder then cools and hardens, creating a strong and durable connection. This process is commonly used in electronics to create electrical connections, but it can also be used in other fields such as plumbing and metalwork.
The importance of wire soldering in creating strong and durable connections cannot be overstated. A well-soldered joint not only ensures the reliability of an electronic device but also its longevity. Poorly soldered joints can lead to a variety of issues, including short circuits, device failure, and even fires. Therefore, understanding and mastering the art of wire soldering is crucial for anyone involved in electronics.
Wire soldering is not just about creating a strong connection, but also about creating a connection that is electrically conductive. The solder used in wire soldering is typically made of a mixture of metals that have low melting points and high electrical conductivity. This ensures that the soldered joint will not only be strong but also able to efficiently conduct electricity.
Basics of Wire Solder
Wire solder is the filler material used in the process of wire soldering. It is typically made of a mixture of metals, such as tin and lead, that have low melting points and high electrical conductivity. The solder is melted onto the joint using a soldering iron, and it then cools and hardens, creating a strong and durable connection.
There are different types of wire solder available on the market, each with its own unique properties and uses. The most common types of wire solder are lead-based solder, lead-free solder, and silver solder. Lead-based solder is the traditional type of solder and is known for its ease of use and strong connections. However, due to health concerns associated with lead, many people now prefer to use lead-free solder. Silver solder, on the other hand, is known for its high electrical conductivity and is often used in high-end audio and video equipment.
When choosing a type of wire solder, it is important to consider the specific needs of your project. For example, if you are soldering a joint that will be subjected to high temperatures, you may want to choose a solder with a high melting point. On the other hand, if you are soldering a delicate electronic component, you may want to choose a solder with a low melting point to avoid damaging the component.
Factors to Consider When Buying Wire Solder
When buying wire solder, there are several factors to consider. One of the most important factors is the material composition of the solder. As mentioned earlier, the most common types of wire solder are lead-based solder, lead-free solder, and silver solder. Each type of solder has its own unique properties and uses, so it is important to choose the right type for your project.
The diameter of the solder wire is another important factor to consider. The diameter of the solder wire can affect the amount of solder that is applied to the joint, which can in turn affect the strength and conductivity of the connection. Therefore, it is important to choose a solder wire with a suitable diameter for your project.
Finally, the flux core of the solder wire is also an important factor to consider. The flux core is a material that is contained within the solder wire and is designed to help the solder flow and adhere to the metal surfaces. A good flux core can greatly improve the quality of the soldered joint, so it is important to choose a solder wire with a high-quality flux core.
Understanding Material Composition
As mentioned earlier, the material composition of the solder is one of the most important factors to consider when buying wire solder. The most common types of wire solder are lead-based solder, lead-free solder, and silver solder.
Lead-based solder is the traditional type of solder and is known for its ease of use and strong connections. However, due to health concerns associated with lead, many people now prefer to use lead-free solder. Lead-free solder is typically made of a mixture of tin and other metals, and while it can be a bit more difficult to work with than lead-based solder, it is a safer option.
Silver solder, on the other hand, is known for its high electrical conductivity and is often used in high-end audio and video equipment. Silver solder is typically more expensive than other types of solder, but it can provide superior performance in certain applications.
Importance of Diameter in Wire Solder
The diameter of the solder wire can have a significant impact on the soldering process. A larger diameter solder wire can deliver more solder to the joint, which can be beneficial for larger joints or joints that require a strong connection. However, a larger diameter solder wire can also be more difficult to control, which can lead to excess solder being applied to the joint.
On the other hand, a smaller diameter solder wire can provide more control over the amount of solder that is applied to the joint. This can be beneficial for smaller joints or delicate electronic components. However, a smaller diameter solder wire may not deliver enough solder to larger joints, which can result in a weak connection.
Therefore, it is important to choose a solder wire with a suitable diameter for your project. If you are unsure about the appropriate diameter, it may be helpful to start with a medium diameter solder wire and then adjust as necessary based on the results.
Understanding Flux Core in Wire Solder
The flux core is a material that is contained within the solder wire and is designed to help the solder flow and adhere to the metal surfaces. The flux core acts as a cleaning agent, removing any oxidation from the metal surfaces and promoting the formation of a strong, electrically conductive joint.
The role of the flux core in soldering is crucial. Without a good flux core, the solder may not flow properly, resulting in a weak or non-conductive joint. Therefore, it is important to choose a solder wire with a high-quality flux core.
There are different types of flux cores available, each with its own unique properties and uses. Some flux cores are designed for general-purpose soldering, while others are designed for specific applications, such as high-temperature soldering or soldering delicate electronic components. Therefore, it is important to choose a flux core that is suitable for your specific needs.
Top Wire Solder Brands
There are many brands of wire solder available on the market, each with its own unique offerings. Some of the top brands include Kester, Alpha, and MG Chemicals. These brands are known for their high-quality products and have a strong reputation in the electronics industry.
When comparing different brands, it is important to consider factors such as the material composition of the solder, the diameter of the solder wire, and the quality of the flux core. Additionally, it may be helpful to read reviews from other users to get a sense of the performance and reliability of the solder.
Ultimately, the best brand of wire solder will depend on your specific needs and preferences. It may be helpful to try out a few different brands to see which one works best for you.
How to Use Wire Solder
Using wire solder is a relatively straightforward process, but it does require some practice to master. The first step is to heat up the soldering iron. Once the soldering iron is hot, you can apply the solder to the joint. The solder should melt upon contact with the joint, creating a pool of liquid solder. The liquid solder will then cool and harden, creating a strong and durable connection.
There are several safety precautions to keep in mind when using wire solder. First and foremost, it is important to wear protective gear, such as safety glasses and gloves, to protect yourself from the heat of the soldering iron and the potentially harmful fumes from the solder. Additionally, it is important to work in a well-ventilated area to ensure that any fumes from the solder are properly dispersed.
Finally, it is important to handle the soldering iron with care to avoid burns. The tip of the soldering iron can reach temperatures of up to 800 degrees Fahrenheit, so it is crucial to handle it with care and to always place it in a safe location when not in use.
Maintaining Wire Solder
Maintaining wire solder is relatively simple, but it is an important part of ensuring the longevity and performance of the solder. One of the most important aspects of maintaining wire solder is proper storage. Wire solder should be stored in a cool, dry place to prevent it from oxidizing. Oxidation can degrade the quality of the solder and make it more difficult to work with.
Another important aspect of maintaining wire solder is regular cleaning. Over time, the flux core can leave a residue on the solder wire, which can affect the quality of the soldered joint. Therefore, it is important to clean the solder wire regularly to remove any residue and maintain the quality of the solder.
Finally, it is important to inspect the solder wire regularly for any signs of damage or degradation. If the solder wire appears to be damaged or degraded, it may be best to replace it to ensure the quality of your soldered joints.
Common Mistakes When Buying Wire Solder
There are several common mistakes that people make when buying wire solder. One of the most common mistakes is not considering the material composition of the solder. As mentioned earlier, the material composition of the solder can have a significant impact on the soldering process and the quality of the soldered joint. Therefore, it is important to choose a solder with a suitable material composition for your project.
Another common mistake is not considering the diameter of the solder wire. The diameter of the solder wire can affect the amount of solder that is applied to the joint, which can in turn affect the strength and conductivity of the connection. Therefore, it is important to choose a solder wire with a suitable diameter for your project.
Finally, many people overlook the importance of the flux core in the solder wire. The flux core plays a crucial role in the soldering process, helping the solder flow and adhere to the metal surfaces. Therefore, it is important to choose a solder wire with a high-quality flux core.
Case Study: Successful Use of Wire Solder
One example of the successful use of wire solder is in the construction of a custom audio amplifier. The builder used silver solder to create the electrical connections in the amplifier, citing its high electrical conductivity as a key factor in the amplifier’s performance.
The builder also noted the importance of using a solder wire with a suitable diameter. They used a smaller diameter solder wire for the delicate electronic components and a larger diameter solder wire for the larger joints. This allowed them to control the amount of solder that was applied to each joint, ensuring a strong and conductive connection.
This case study highlights the importance of choosing the right wire solder for your project. By considering factors such as the material composition of the solder, the diameter of the solder wire, and the quality of the flux core, you can ensure the success of your soldering projects.
Future Trends in Wire Soldering
As technology continues to evolve, so too does the field of wire soldering. One of the most notable trends in wire soldering is the increasing use of lead-free solder. This trend is driven by health concerns associated with lead, as well as regulations in many countries that restrict the use of lead in electronics. As a result, many manufacturers are now producing high-quality lead-free solder that is easy to work with and provides strong and durable connections.
Another trend in wire soldering is the increasing use of automated soldering machines. These machines can solder joints with high precision and consistency, making them ideal for mass production. However, manual soldering is still crucial for custom projects and repairs, where the flexibility and adaptability of a human operator are required.
These trends will likely continue to shape the field of wire soldering in the coming years. As such, it is important for anyone involved in electronics to stay up-to-date with the latest developments in wire soldering.
Conclusion
Wire soldering is a crucial skill in the world of electronics, playing a key role in the creation of durable and reliable electrical connections. Understanding the basics of wire soldering, including the different types of wire solder and the factors to consider when buying wire solder, is essential for anyone involved in electronics.
By choosing the right wire solder for your project, using it properly, and maintaining it correctly, you can ensure the success of your soldering projects. Additionally, by avoiding common mistakes when buying wire solder and staying up-to-date with the latest trends in wire soldering, you can further enhance your soldering skills.
In conclusion, wire soldering is a fundamental aspect of electronics that should not be overlooked. Whether you are a hobbyist, a professional, or a student, mastering the art of wire soldering can greatly enhance your electronics projects and open up new possibilities for creativity and innovation.
FAQ
What is wire soldering?
Wire soldering is a technique used to join together two or more metal items by melting a filler material, known as solder, onto the joint. The solder then cools and hardens, creating a strong and durable connection.
What are the different types of wire solder?
The most common types of wire solder are lead-based solder, lead-free solder, and silver solder. Each type of solder has its own unique properties and uses.
What factors should I consider when buying wire solder?
When buying wire solder, you should consider factors such as the material composition of the solder, the diameter of the solder wire, and the quality of the flux core.
How do I use wire solder?
To use wire solder, you first heat up the soldering iron. Once the soldering iron is hot, you can apply the solder to the joint. The solder should melt upon contact with the joint, creating a pool of liquid solder. The liquid solder will then cool and harden, creating a strong and durable connection.
What are some common mistakes when buying wire solder?
Some common mistakes when buying wire solder include not considering the material composition of the solder, not considering the diameter of the solder wire, and overlooking the importance of the flux core in the solder wire.