Plastic welders are an indispensable tool in various industries, from automotive repair to plumbing and construction. They are used to join plastic materials together, creating a bond that is as strong, if not stronger, than the original material. The importance of plastic welders cannot be overstated, as they provide a cost-effective and efficient solution for repairing and fabricating plastic parts.
The purpose of this article is to provide a comprehensive guide on plastic welders. It aims to educate readers on the importance of plastic welding, the different types of plastic welders, and how to choose the right one. It also provides safety precautions, maintenance tips, and future trends in plastic welding technology.
Whether you are a professional looking to enhance your skills, a hobbyist interested in DIY projects, or a consumer wanting to make an informed purchase, this article will provide valuable insights into the world of plastic welding.
Our Top Plastic Welder Picks
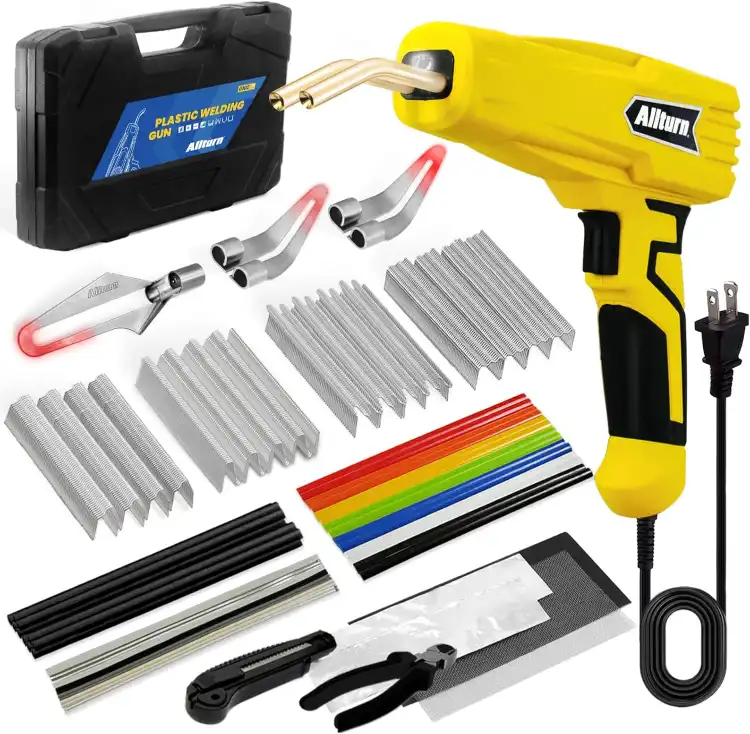
Allturn Upgraded Plastic Welder
Check on AmazonKey Specs:
- Power: 110V, 100W
- Temperature: Up to 1380°F for staples, 900°F for smoothing tip
- Welding Staples: 800 staples included (200 flat, wavy, M-type, V-type)
- Ergonomics: TPR material handle for comfort
- Warranty: 1-year guarantee, internal overheating protection
The Allturn Upgraded Plastic Welder is a fantastic tool for anyone who works with plastics, especially for automotive repairs like car bumpers. I really appreciate how quick and efficient the welder is—reaching temperatures up to 1380°F for the staples and 900°F for the smoothing tip within seconds. The ergonomic design ensures comfort during extended use, while the included accessories, like 800 staples and multiple welding rods, make it versatile for a wide range of projects. Its patented design sets it apart in functionality and style.
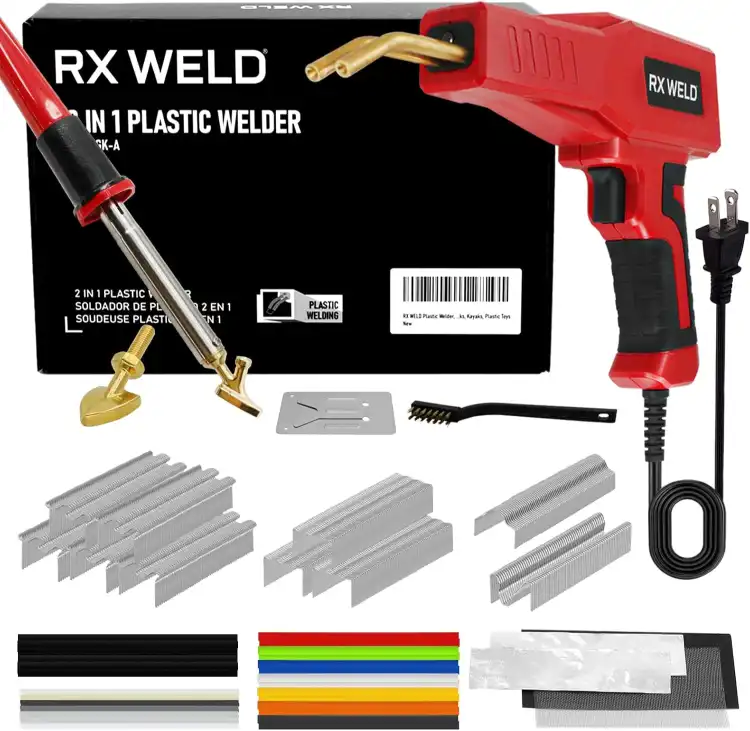
RX WELD Plastic Welder
Check on AmazonKey Specs:
- Power: 110V-120V, 100W
- Temperature: Up to 800°F
- Accessories: Includes 1000PCS hot staples
- Applications: Ideal for car bumpers, dashboards, kayaks, and more
- Warranty: 1-year quality guarantee
The RX WELD Plastic Welder kit is a solid, versatile choice for anyone who needs to repair plastic items such as car bumpers or kayaks. I love the combination of the plastic welding gun and soldering iron, making it a complete package for both repairing cracks and smoothing out scars. It reaches a maximum temperature of 800°F in just five minutes, allowing for quick and efficient work. The 1-year warranty gives extra peace of mind, and the adjustable temperature feature adds precision.
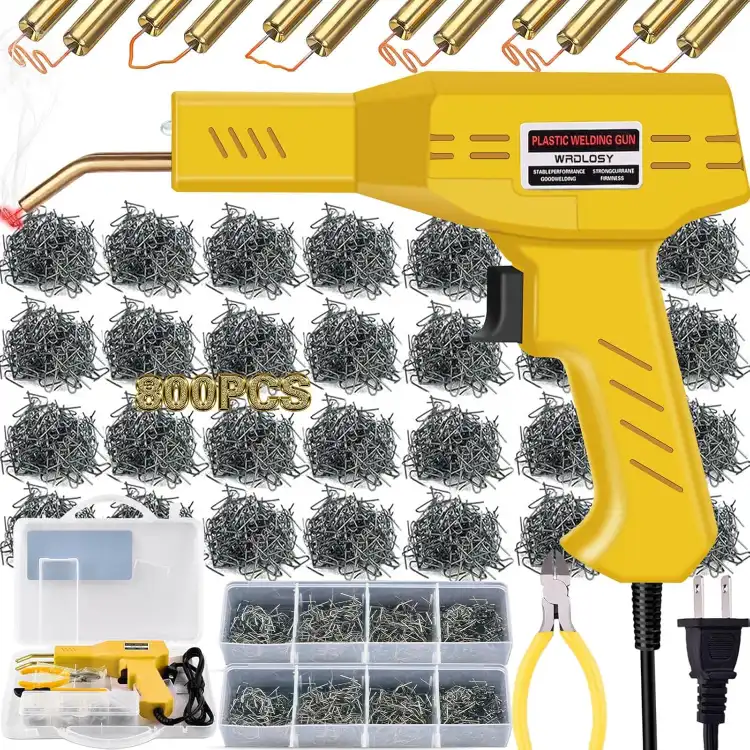
Plastic Welder, 800PCS Staples, Plastic Welding Kit
Check on AmazonKey Specs:
- Included Staples: 800PCS (variety of designs)
- Power: Instant On/Off functionality
- Materials: Stainless steel staples
- Design: Ergonomic with built-in light
- Warranty: 5-year worry-free guarantee
The WRDLOSY Plastic Welder Kit is an excellent tool for DIY enthusiasts and professionals alike. With 800 staples included, it offers a wide range of options for repairing different types of plastics. The ergonomic design ensures comfort during long repairs, and the quick operation process makes it efficient. I particularly like the stainless steel staples that won’t rust, providing a long-lasting fix. This kit is ideal for car bumpers, kayaks, and other everyday plastic repairs.
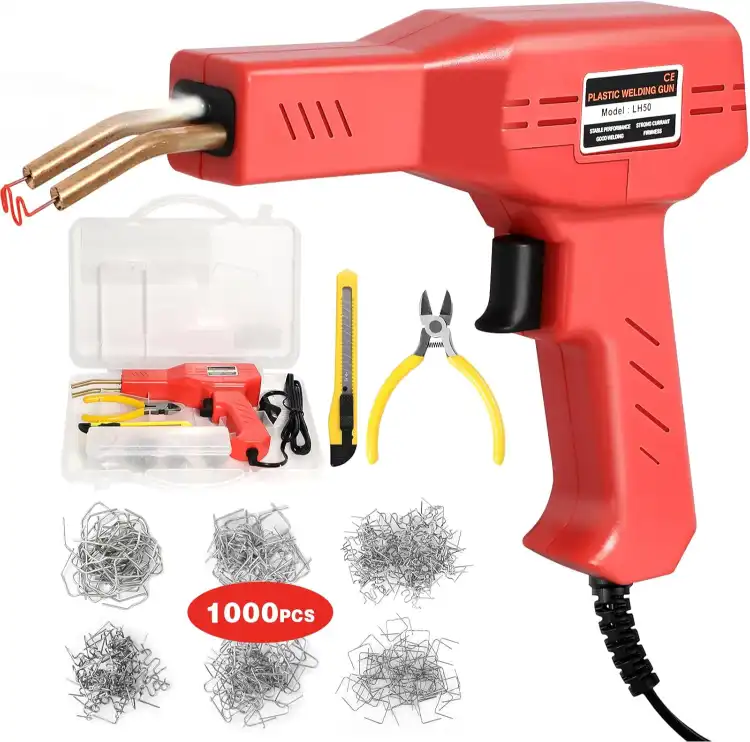
ATOLS Plastic Welder
Check on AmazonKey Specs:
- Staples: 1000PCS, includes 6 types
- Power: Rapid heating in 1-2 seconds
- Materials: Stainless steel staples
- Design: Ergonomic, rubber handle
- Included Items: Carry case, pliers, multiple staple types
The ATOLS Plastic Welder Kit is a must-have for anyone looking to repair a wide range of plastics. With 1000 staples and 6 staple types, it’s designed to handle 98% of plastics. The rapid heating feature ensures quick repairs, while the ergonomic design makes it comfortable for extended use. The inclusion of a built-in light enhances precision, especially in dim environments. Ideal for car bumpers, dashboards, and other automotive parts, this kit is easy to use and highly reliable.
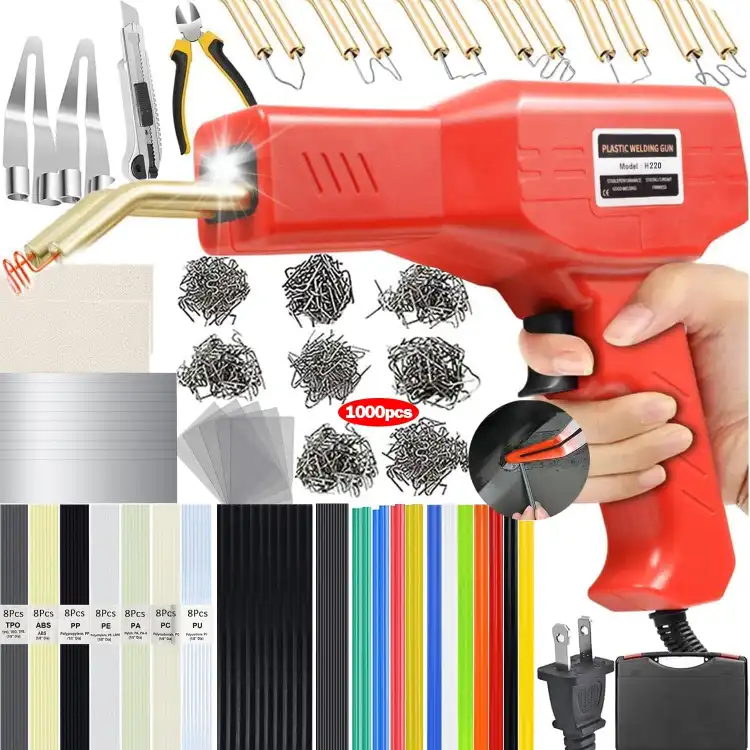
Upgraded 220W Plastic Welder
Check on AmazonKey Specs:
- Power: 220W rapid heating
- Included Staples: 1000PCS, 6 types
- Welding Rods: 100PCS, compatible with various plastics
- Design: Heat-resistant handle, LED light
- Safety: Overheat protection device
The VCTSELITY 220W Plastic Welder Kit offers excellent value for anyone looking to repair plastic surfaces, especially car bumpers and dashboards. With a powerful 220W heating system, it quickly melts staples or plastic rods for fast, secure repairs. The kit includes 1000PCS staples and 100PCS welding rods, covering a wide range of plastics like ABS, PP, and TPO. Its heat-resistant handle and LED light enhance comfort and precision. The overheat protection ensures safety, making this a reliable tool for DIY plastic repairs.
Understanding Plastic Welding
Plastic welding is a process that involves the use of heat to melt the joining surfaces of two or more plastic parts. The melted surfaces are then brought together and allowed to cool, resulting in a fusion of the parts. This process is similar to metal welding, but it uses lower temperatures and different equipment.
The importance of plastic welding in repairs is significant. It allows for the restoration of damaged plastic parts, saving costs on replacement. It is also used in the fabrication of new parts, making it a versatile process in various industries.
Understanding plastic welding is crucial for anyone involved in the repair or fabrication of plastic parts. It requires knowledge of the different types of plastics, the appropriate welding techniques, and the right equipment to use. With the right skills and tools, plastic welding can be a valuable asset in any repair or manufacturing process.
The Basics of Plastic Welding
The process of plastic welding involves several steps. First, the surfaces to be joined are cleaned and prepared. Then, heat is applied to the surfaces using a plastic welder. The surfaces are then brought together and allowed to cool, forming a strong bond.
There are different types of plastic welding, each suitable for different applications. Some of the most common types include hot gas welding, ultrasonic welding, and friction welding. Hot gas welding is often used for repairing plastic parts, while ultrasonic and friction welding are commonly used in manufacturing processes.
Understanding the basics of plastic welding is essential for anyone looking to use a plastic welder. It requires knowledge of the different welding techniques, the appropriate heat settings, and the correct welding speed. With the right knowledge and practice, anyone can master the art of plastic welding.
The Need for Plastic Welders
Plastic welders are necessary tools in various industries. They are used to repair damaged plastic parts, fabricate new parts, and join plastic materials together. Without plastic welders, these tasks would be difficult, if not impossible, to accomplish.
Common uses of plastic welders include repairing plastic parts in cars, motorcycles, and other vehicles. They are also used in plumbing to repair and install plastic pipes. In the construction industry, plastic welders are used to join plastic sheets and other materials.
The need for plastic welders extends beyond professional use. They are also useful for DIY enthusiasts and hobbyists who enjoy working on their own projects. Whether it’s repairing a broken plastic chair or creating a custom plastic part, a plastic welder can be a valuable tool in any workshop.
Types of Plastic Welders
There are various types of plastic welders available on the market, each with its own set of features and benefits. Some of the most common types include hot air welders, ultrasonic welders, and laser welders.
Hot air welders use a stream of hot air to melt the plastic, making them suitable for a wide range of applications. Ultrasonic welders use high-frequency sound waves to generate heat, making them ideal for welding thin and delicate plastic parts. Laser welders use a focused laser beam to melt the plastic, providing a high level of precision and control.
Each type of plastic welder has its pros and cons. Hot air welders are versatile and easy to use, but they may not be suitable for delicate parts. Ultrasonic welders provide a high level of precision, but they can be expensive. Laser welders offer the highest level of control, but they require a significant investment. Understanding these pros and cons can help you choose the right plastic welder for your needs.
Factors to Consider When Buying a Plastic Welder
When buying a plastic welder, there are several factors to consider. The price is an important consideration, as plastic welders can range from affordable to expensive. However, it’s important to remember that the cheapest option may not always be the best in terms of quality and performance.
The quality of the plastic welder is another important factor. A high-quality welder will provide a strong and durable bond, ensuring the longevity of the repaired or fabricated part. It’s also important to consider the brand reputation. Brands with a good reputation are likely to provide reliable and high-performing products.
User reviews can also provide valuable insights into the performance and reliability of a plastic welder. They can highlight any potential issues or drawbacks, helping you make an informed decision. However, it’s important to take these reviews with a grain of salt, as they can sometimes be biased or inaccurate.
Understanding the Specifications of Plastic Welders
Understanding the specifications of plastic welders can help you choose the right one for your needs. Some of the common specifications include the power output, temperature range, and welding speed.
The power output determines the amount of heat the welder can produce, affecting the speed and efficiency of the welding process. The temperature range indicates the range of temperatures the welder can operate at, affecting its versatility and suitability for different types of plastics. The welding speed refers to the speed at which the welder can join the plastic parts, affecting the quality and strength of the bond.
Each specification is important in its own way, and understanding them can help you choose a plastic welder that meets your needs. For example, if you need a welder for heavy-duty applications, you might want to choose one with a high power output and a wide temperature range. On the other hand, if you need a welder for delicate parts, you might want to choose one with a low welding speed and a narrow temperature range.
Safety Precautions When Using Plastic Welders
Using a plastic welder involves certain risks, and it’s important to take safety precautions to protect yourself and others. One of the most important precautions is to wear safety gear. This includes safety glasses to protect your eyes from sparks and debris, gloves to protect your hands from heat and burns, and a respirator to protect your lungs from harmful fumes.
Safe operation practices are also crucial when using a plastic welder. This includes operating the welder in a well-ventilated area to prevent the buildup of harmful fumes, keeping the welder away from flammable materials to prevent fires, and turning off the welder when not in use to prevent accidental burns or fires.
Maintenance is another important aspect of safety. Regular maintenance can prevent malfunctions and accidents, ensuring the safe and efficient operation of the plastic welder. This includes cleaning the welder regularly, checking for any signs of damage or wear, and replacing any worn or damaged parts.
Maintenance of Plastic Welders
Regular maintenance of plastic welders is crucial for their longevity and efficiency. This includes cleaning the welder after each use to remove any residue or debris, checking the welder regularly for any signs of damage or wear, and replacing any worn or damaged parts.
The importance of maintenance cannot be overstated. A well-maintained plastic welder will perform better, last longer, and be safer to use. It can also save you money in the long run by preventing costly repairs or replacements.
Maintenance practices can vary depending on the type of plastic welder. For example, hot air welders may require regular cleaning of the heating element, while ultrasonic welders may require regular inspection of the sound waves. It’s important to follow the manufacturer’s instructions for maintenance to ensure the proper care of your plastic welder.
Top Plastic Welder Brands
There are several top brands in the plastic welder market, each offering a range of products with different features and benefits. Some of the most popular brands include Leister, Dukane, and Branson.
Leister is known for its high-quality hot air welders, which are widely used in various industries. Dukane offers a range of ultrasonic welders, known for their precision and efficiency. Branson is a leading brand in the laser welding market, offering high-performance products with a high level of control.
Each brand offers a range of products, and it’s important to compare them to find the one that best meets your needs. Factors to consider include the type of welder, the specifications, the price, and the brand reputation. By comparing different brands and products, you can make an informed decision and choose the right plastic welder for your needs.
Case Study: Effective Plastic Repairs with Specific Plastic Welder
One example of an effective plastic repair using a specific plastic welder is the repair of a cracked plastic bumper on a car. The repair was done using a hot air welder from Leister, which is known for its high-quality products.
The repair involved cleaning the cracked area, applying heat with the hot air welder, and then pressing the surfaces together to form a bond. The result was a strong and durable repair that restored the bumper to its original condition.
The chosen plastic welder was effective for this repair due to its high power output and wide temperature range. It was able to melt the plastic quickly and efficiently, allowing for a quick and effective repair. This case study highlights the importance of choosing the right plastic welder for the job.
Common Mistakes to Avoid When Buying a Plastic Welder
When buying a plastic welder, there are several common mistakes to avoid. One of the most common mistakes is choosing a welder based solely on price. While price is an important consideration, it’s also important to consider the quality and performance of the welder.
Another common mistake is not considering the type of plastic you will be welding. Different types of plastics require different types of welders, and choosing the wrong one can result in ineffective or damaging welding.
A third common mistake is not considering the brand reputation. Brands with a good reputation are likely to provide reliable and high-performing products, and choosing a lesser-known brand can be a risky decision.
By avoiding these common mistakes, you can make an informed decision and choose the right plastic welder for your needs.
Future Trends in Plastic Welding Technology
As with any technology, plastic welding is constantly evolving. Current trends in the market include the increasing use of automation and the development of more efficient and versatile welding techniques.
Automation is becoming increasingly common in plastic welding, with many manufacturers offering automated welding systems. These systems can increase efficiency and consistency, reducing the risk of human error and increasing productivity.
Another trend is the development of more efficient and versatile welding techniques. This includes the development of new types of welders, such as laser welders, which offer a high level of precision and control. It also includes the development of new welding techniques, such as friction stir welding, which can join different types of plastics together.
Looking to the future, it’s likely that these trends will continue. We can expect to see further advancements in automation and welding techniques, making plastic welding even more efficient and versatile. This will open up new possibilities for the repair and fabrication of plastic parts, benefiting various industries.
Conclusion
In conclusion, plastic welders are an essential tool in various industries, providing a cost-effective and efficient solution for repairing and fabricating plastic parts. Understanding the basics of plastic welding, the different types of plastic welders, and how to choose the right one is crucial for anyone involved in the repair or fabrication of plastic parts.
With the right knowledge and skills, anyone can master the art of plastic welding. Whether you are a professional looking to enhance your skills, a hobbyist interested in DIY projects, or a consumer wanting to make an informed purchase, this guide provides valuable insights into the world of plastic welding.
As technology continues to evolve, we can expect to see further advancements in plastic welding. This will open up new possibilities for the repair and fabrication of plastic parts, benefiting various industries and making plastic welding an even more valuable skill to have.
FAQ
What is plastic welding?
Plastic welding is a process that involves the use of heat to melt the joining surfaces of two or more plastic parts. The melted surfaces are then brought together and allowed to cool, resulting in a fusion of the parts.
Why are plastic welders necessary?
Plastic welders are necessary tools in various industries. They are used to repair damaged plastic parts, fabricate new parts, and join plastic materials together. Without plastic welders, these tasks would be difficult, if not impossible, to accomplish.
What are the different types of plastic welders?
There are various types of plastic welders available on the market, each with its own set of features and benefits. Some of the most common types include hot air welders, ultrasonic welders, and laser welders.
What factors should I consider when buying a plastic welder?
When buying a plastic welder, there are several factors to consider. These include the price, the quality of the welder, the brand reputation, and user reviews.
What are the safety precautions when using a plastic welder?
Safety precautions when using a plastic welder include wearing safety gear, operating the welder in a well-ventilated area, keeping the welder away from flammable materials, and performing regular maintenance.